Quote:
Originally Posted by redsupra
...6. The advice from the guy at Suprastore.com was to solder the connection. In the end it's up to the auto elec, he's the expert so he did what he knows best...
|
The guy from Suprastore.com was wrong. Solder should never be used on automotive connnections. It's all in TSRM Electrical manual. Those soldered connections seem to work okay for awhile, then they fail due to vibration over time. HOWEVER this assumes you (or your "mechanic") have the tools necessary to do a
proper crimp joint.
Here are the types of wiring splices generally seen in automotive work, ordered from best to worst:
- ROCK-SOLID RELIABLE PROPER CRIMP - USED BY TOYOTA, MERCEDES, BOEING and LOCKHEED MARTIN (etc.)!
- Step 1: Materials

- Step 2: The Right Crimp Tool
(ratcheting, with interchangeable dies):

- The Result:


.
- UNRELIABLE SOLDER JOINT* (for ANY/ALL moving vehicles):
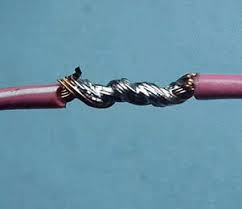
.
- CRAPPY CRIMP (EVEN MORE UNRELIABLE THAN SOLDER):


.
- ABSOLUTELY TERRIBLE!!!
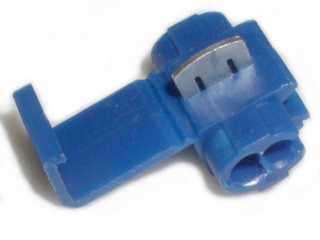
.
- THE WORST - JUST TWIST UP THEM WIRES REAL GEUD, AND IT'LL HOLD FER-SHER:
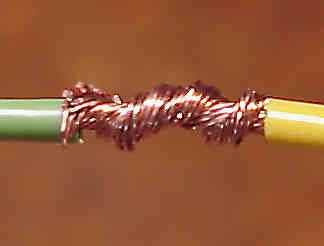
*Note: Soldering is just fine for solid state applications, like circuit boards, and stationary applications (like home stereo wiring). The unreliability comes when vibration and movement is applied to the place along the wire where the solder wicking ends (typically up under the insulation, making it extremely difficult to troubleshoot).